I had taken the two part pole for booming out the Whimbrel’s headsails home for refurbishment as the ‘main’ part looked distinctly crabby.
Once dismantled I set too with a heat gun to strip the main pole of varnish. I quickly discovered the dreaded rot. The pole had to have a section cut off its outer end a few seasons back due to the very same. It had ‘collapsed’ whilst sailing with my youngest sibling as crew. At the time the wood looked good beyond the cutback.
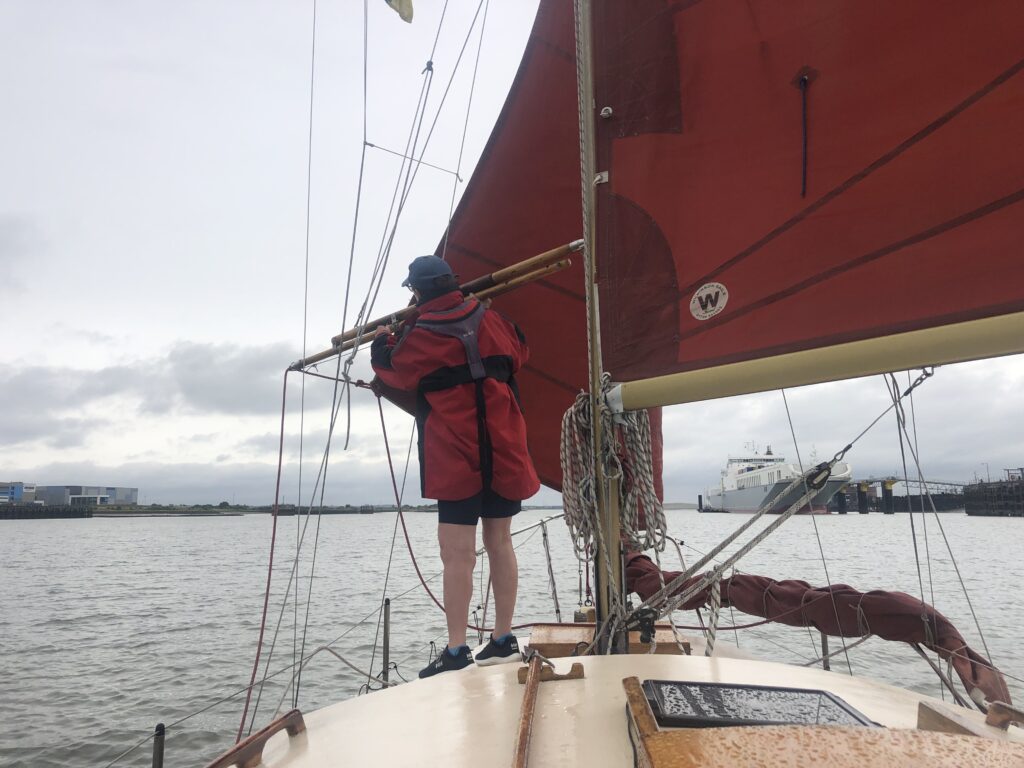
This time it was terminal: the rot was in the middle area and along its length to outer end. It seemed to run down the centre of the original tree.
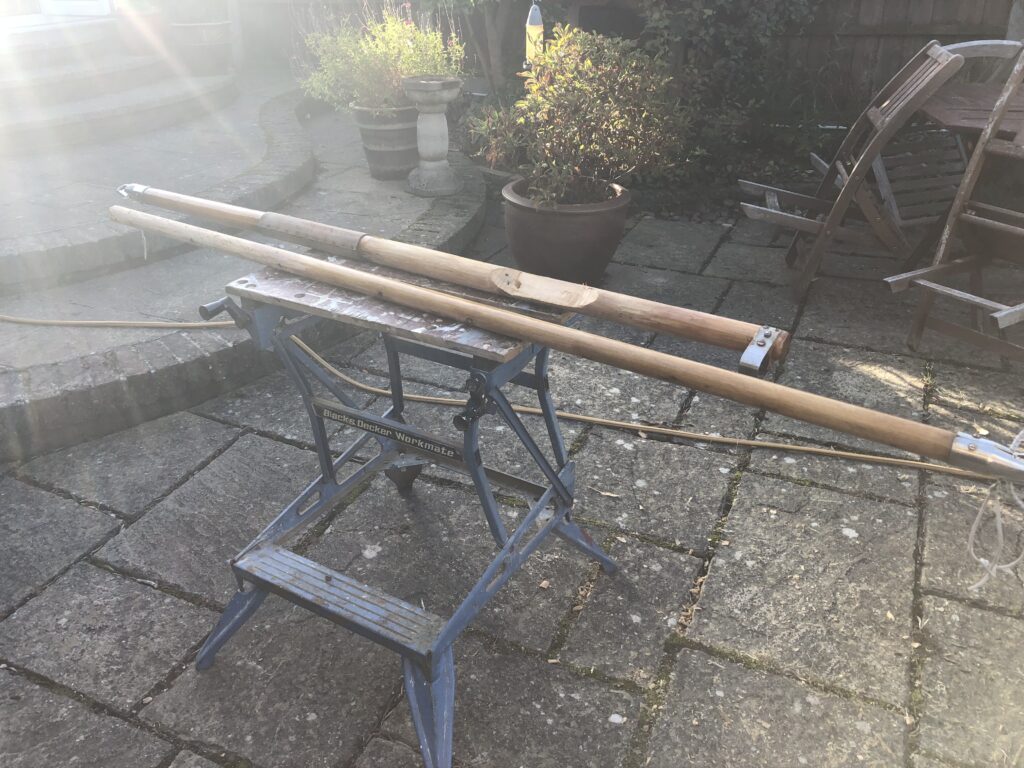
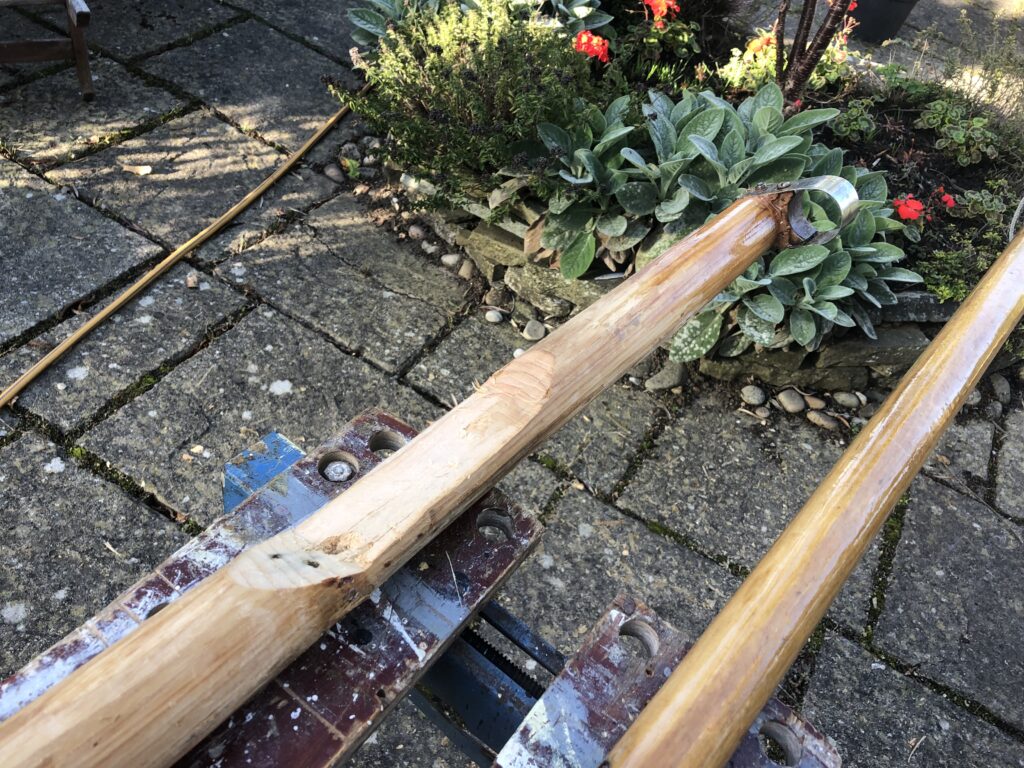
The main pole was initially made from a piece of Sitka Spruce I obtained from a long closed wood merchant in South Benfleet – they were general builders merchants but had other stuff in small quantities.
The outer pole is designed to run in housings I made from stainless steel and is secured by a pin.
I researched on line for suitable timber – it could be ordered at great expense. So, thinking that a couple of the Maldon boatyards might have some, I had a wander. Jim at Downs Road Yard had some pieces of Douglass Fir from a mast project but they were not of sufficient length, when section was good! So, onto the next yard. Scouting round the Shipways Yard by Marine Store, I spotted some suitable timber – the yard asked me to come back in a a couple of days and Adrian (manager – and boat builder/repairer) would sort me out…
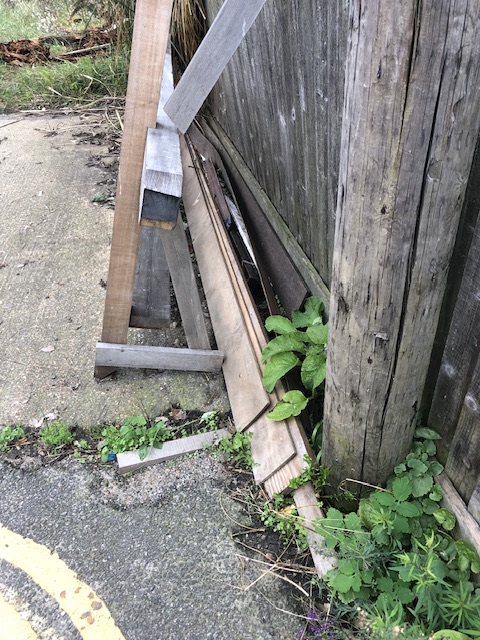
Returning to the Shipways Yard, Adrian remembered me (and the mate) from a couple of visits over recent years staying at the yards visitor berth. We had a natter about ‘the Finesse’ – it transpired that he had been the man who converted F24, No.5, Mariette to gaff rig some fifteen years ago. Adrian was saddened to hear that the boat, as far as I knew, has been languishing in a rill at the Benfleet YC. Hey Ho!
Anyway, Adrian grabbed a couple of planks from a little pile of spruce planking and after ascertaining that I had neither a band saw or planer he proceeded to reduce the ‘grey’ boards of spruce to a number of battens making up a little over the finished size of the pole… Thirty quid!
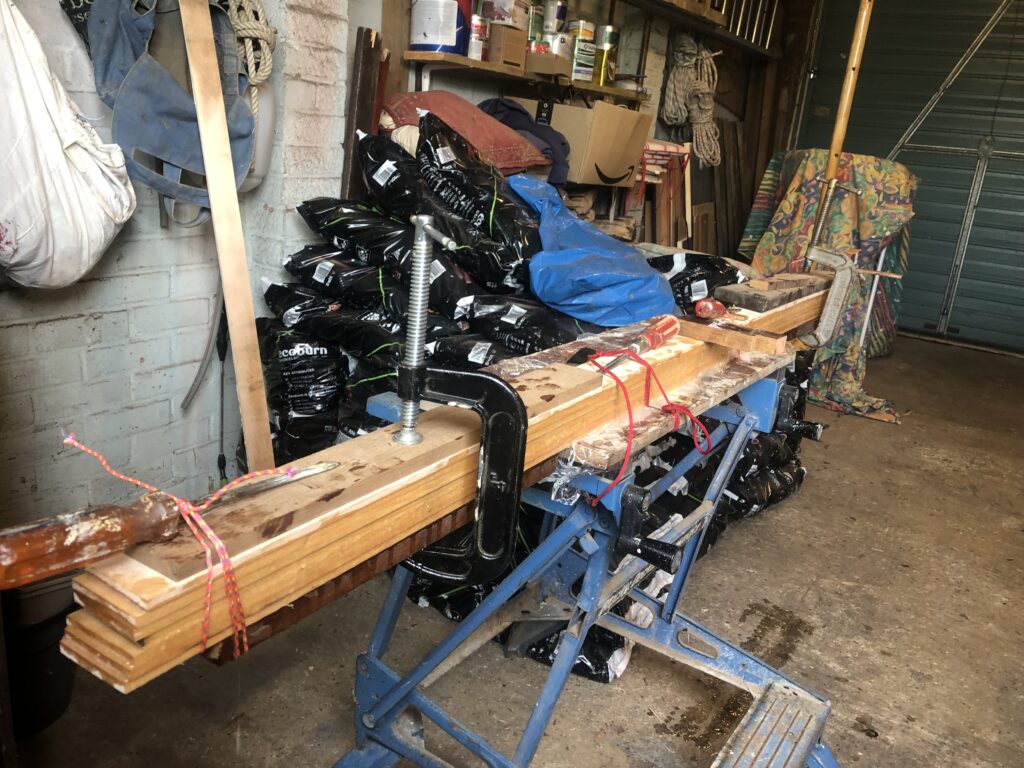
I had to order up a West epoxy kit and as soon as it was delivered the battens were set up on a bench then glued and clamped.
The glued assemblage was left to cure for a couple of days before I set to and began squaring off. Our ‘boy’ who was fortunately working from his home popped over with his rudimentary but effective planer which saved some graft!
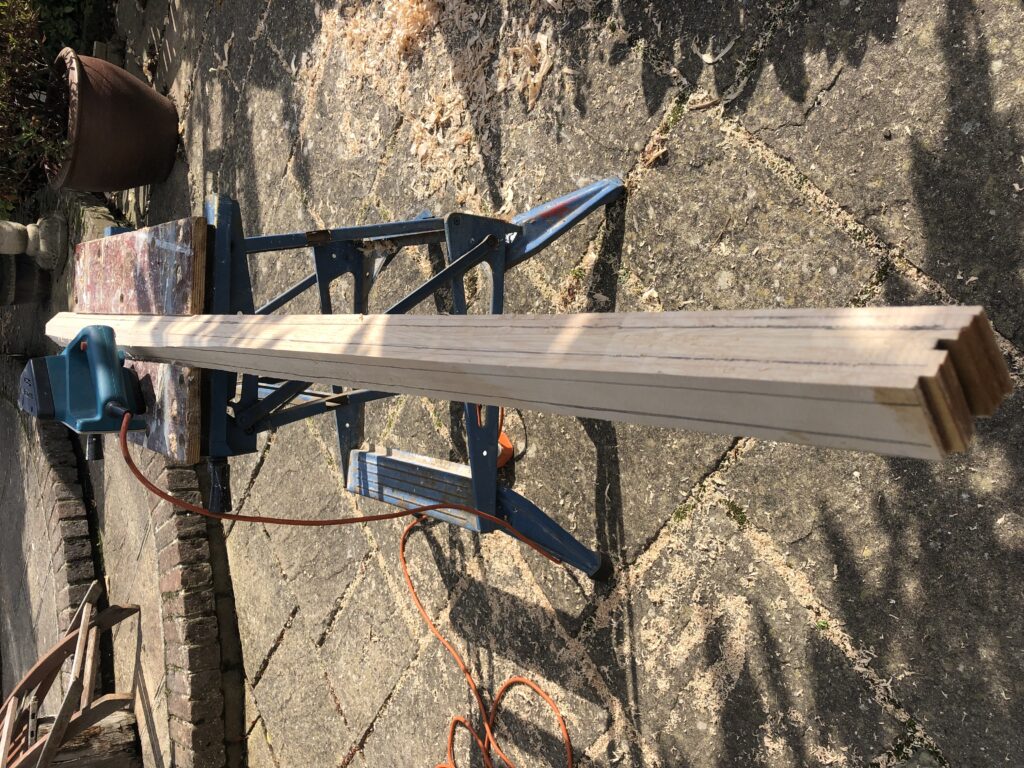
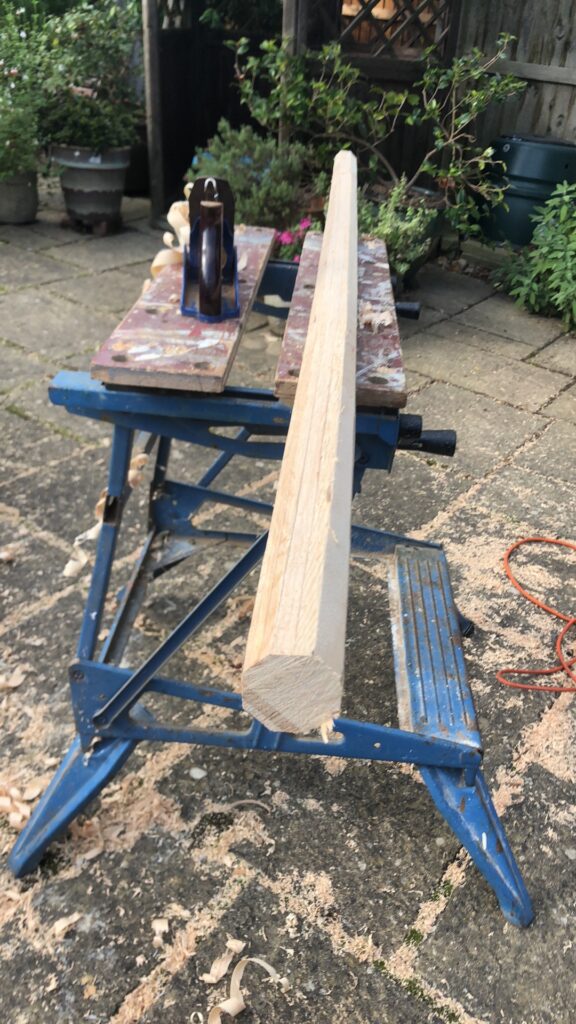
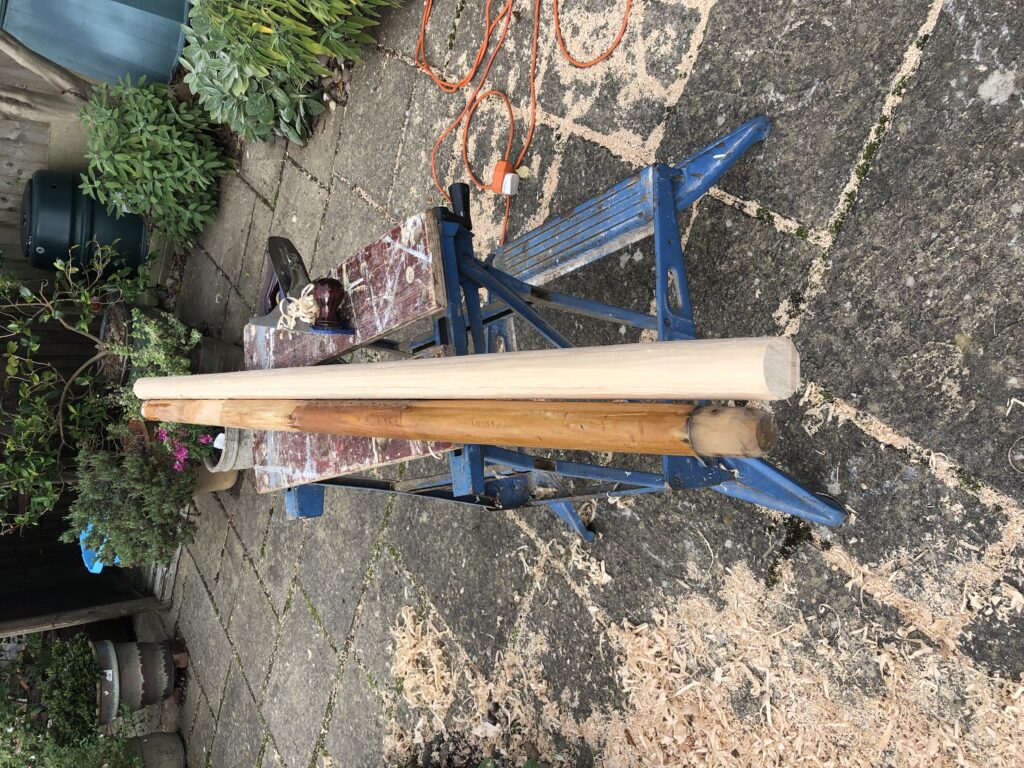
Once all the shaping with plane and then a spoke-shave was done, the pole was sanded until I was satisfied it looked and felt right.
The next job was to reassemble the housings for the outer sliding pole. Fortunately, I had been able to remove these without damaging them and a quick sand to remove old epoxy glue and they were ready.
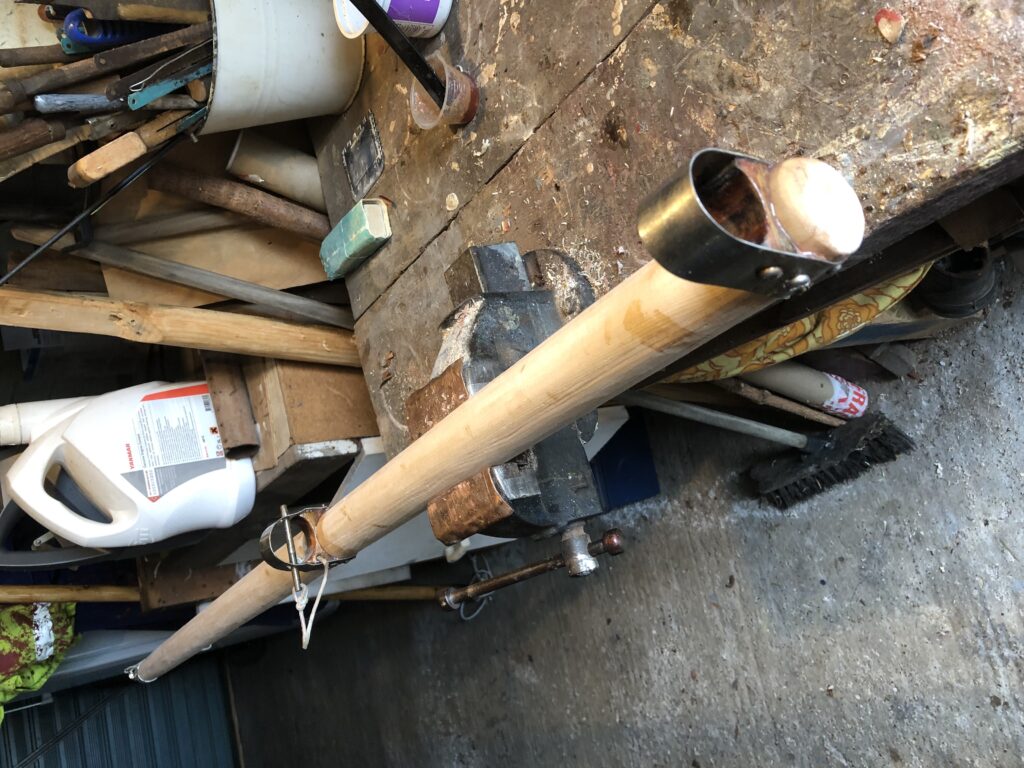
The inner end where the mast fitting was to be fitted was given several coats of varnish prior to its final securing. That done, it was over to the varnish brush and a steady daily build up of eight coats of urethane varnish.
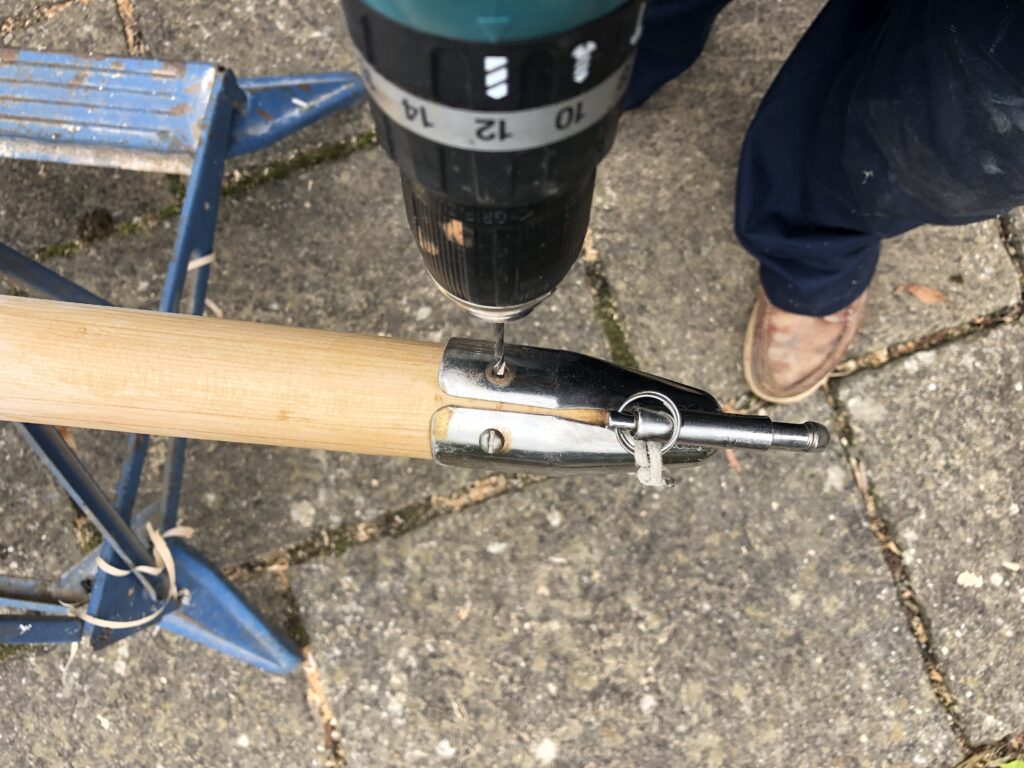
Once the varnishing was completed the new pole was re-leathered where the pole can come up against the forward mast stays.
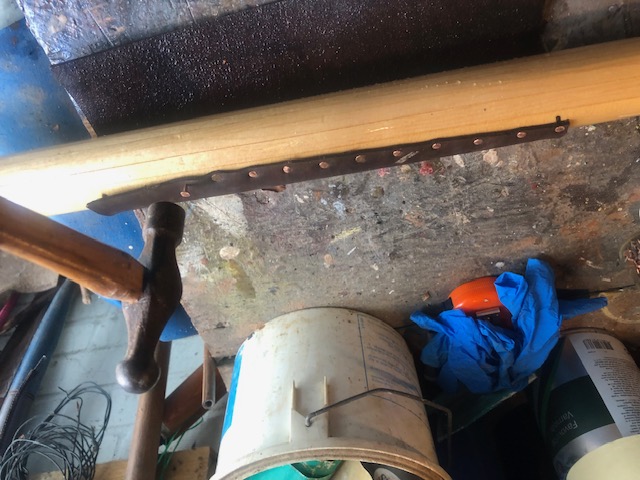
The set up was originally a single pole made from the boom of Mirror dinghy 959 dating back to 1963, which I had played with for many years of childhood, as had my siblings too. The dinghy ultimately came my way and even Christobel ‘enjoyed’ a few jaunts out in it…
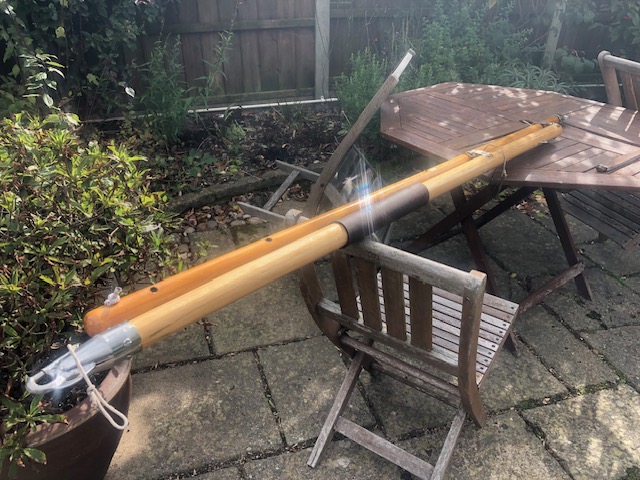
Within a short time, I decided that an extending booming out pole was required but did not want to go for the typical aluminium poles seen aboard cruisers. It was a kind of ‘magic moment’ when I contrived the idea of a sliding assembly in housings similar to the system in use on spritsail barges for housing and lowering of topmasts.
Oft referred to as, ‘You Play with Your Toy, I’ll steer…’ by the mate, it has worked extremely well with its adjustment ability to suit set of both the working jib and Genoa.
It was an interesting project. The laminations of the new pole are visible after varnishing and it all looks very strong: ready for the next thirty years, or so…